In collaboration with Center Parcs, the Limburgse Reconversie Maatschappij (LRM or Société de reconversion du Limbourg) aimed to build a luxury holiday park on the former mining site in the Meuse valley. The place had, according to the LRM, enormous potential to become a real tourist attraction. The project has given pride of place to EQUITONE [tectiva] panels. Bart Moors, Project Manager at Tractebel, explains how the Terhills Resort was born and how the terms circularity and modularity were incorporated.
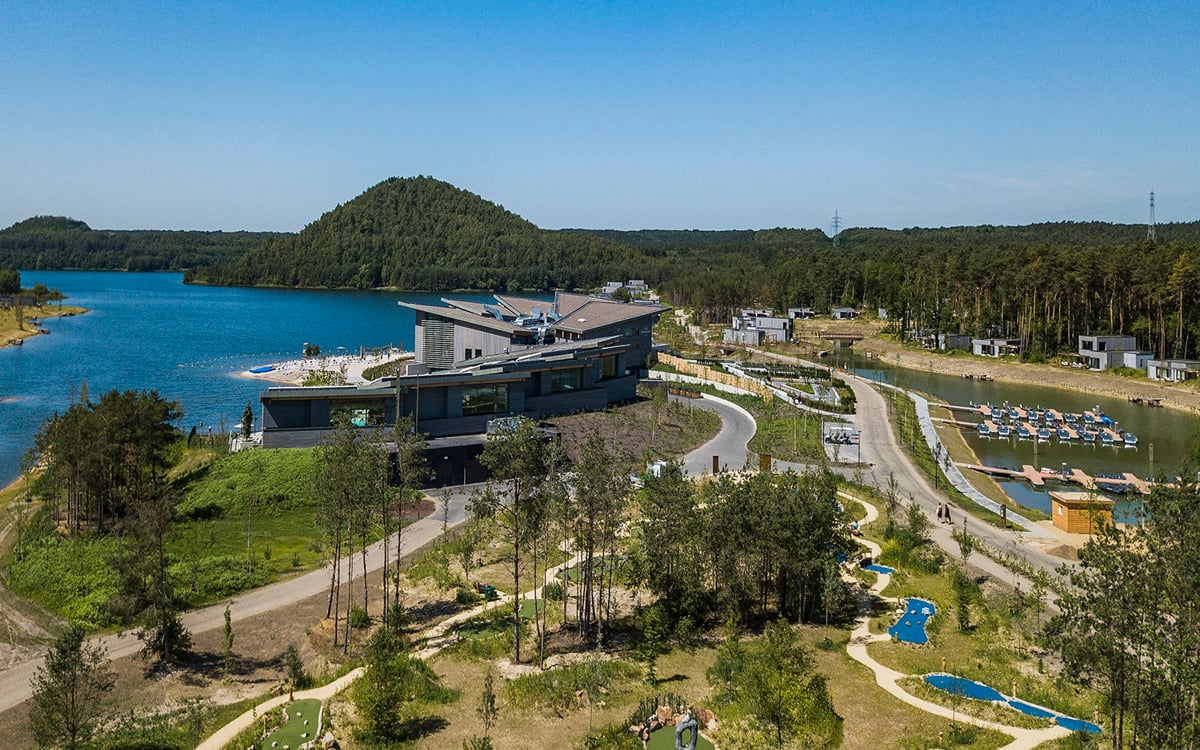
Terhills mining past
The name “Terhills” refers to the site's mining past. The shape of the landscape is indeed the result of many years of extraction in the mine. In addition to the characteristic slag heaps, the water bodies represent a distant reminder of the gravel extractions that took place there in the past. With this project, the LRM and Center Parcs wanted to address a market segment different from other Limburg parks, hence the idea of creating a luxury resort.
Photo : Sourbron Fotografie
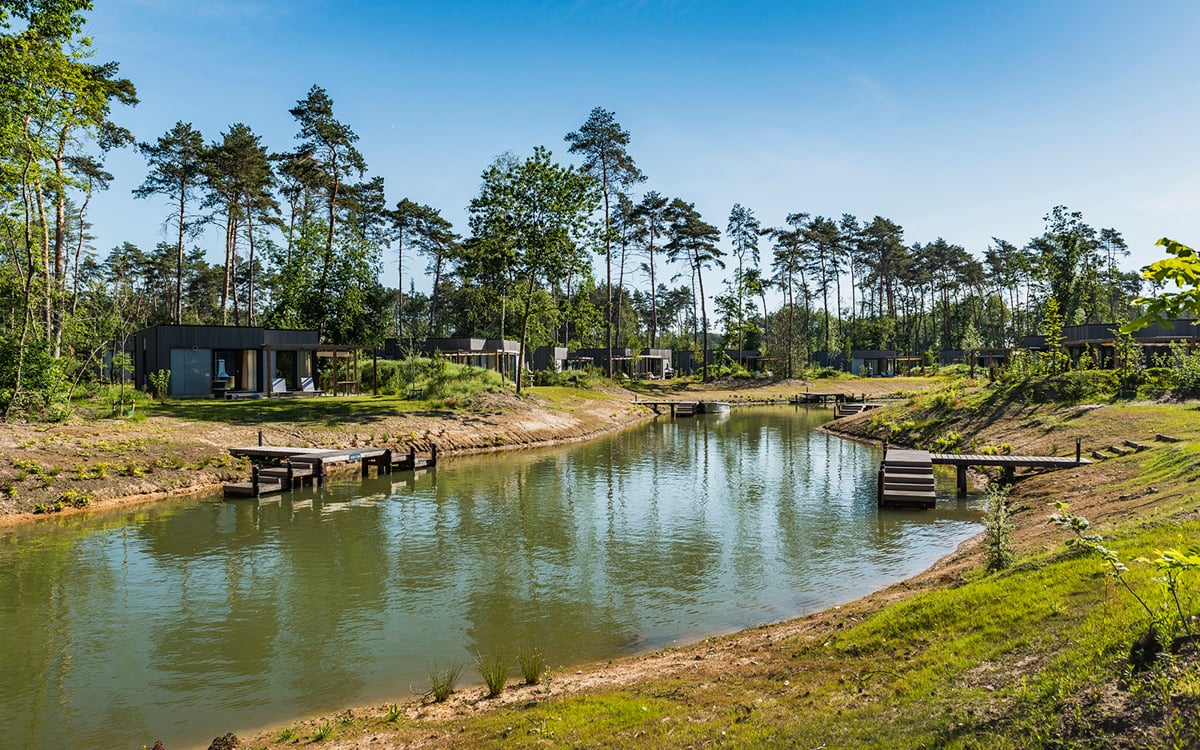
Luxurious Center Parcs resort
“With the LRM and Center Parcs, the architectural firm Zeelenberg imagined a resort with a special connection to water. LRM was looking for a multidisciplinary partner for the execution of the entire project - infrastructure, landscaping, technical, stability, project management, architecture and interior included - and called on Tractebel to collaborate with Luc Buelens, Seto and LST. Concretely, Tractebel's mission consisted of building a resort with all the infrastructure works, waterways, 250 housing units, a facility building and a central meeting space, ”explains Bart Moors of Tractebel.
Photo : Sourbron Fotografie
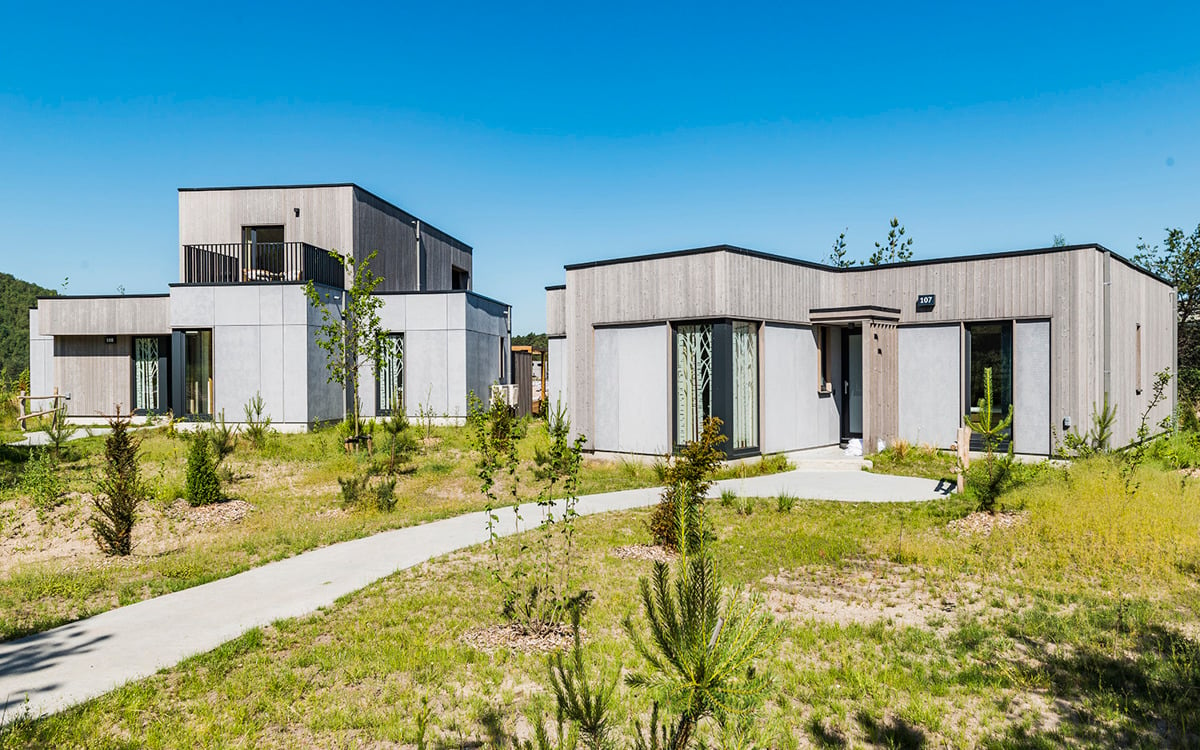
250 prefabricated houses
“My colleagues Nicole Akkermans, Jeroen Van der Velden, Erik Craps and I transformed the LRM conceptual project into a draft, an environmental request and dossiers ready for adjudication. The goal was really to deliver a quality product. We also wanted each house to have a good location in relation to the forest and the water. In addition, everything had to be done in a relatively short period of time, which is why we opted for prefabricated elements and a wooden frame. The prefabrication went very well and allowed us to make a minimum of mistakes. Thanks to the model villas built as part of a first phase, We were thus able to detect a few points for improvement and make small adjustments in time before having the 250 housing units manufactured. The challenge in this project really lay in the number of dwellings. If you make a mistake in a house, you get the same error 250 times and you can also multiply the cost by 250. In the end, everything went well, but it still gave us a lot of headaches ” adds Bart Moors.
Photo : Sourbron Fotografie
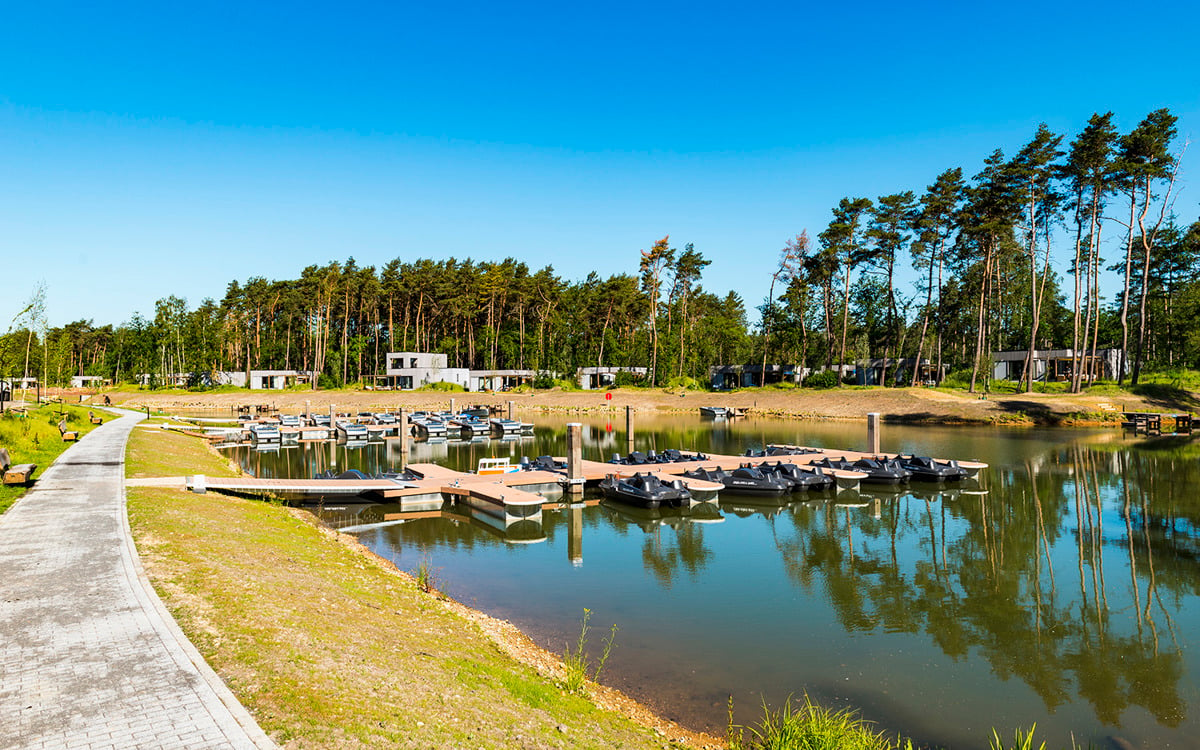
Different types of houses
Visitors can drive their car to the front door to unload their luggage. They are then invited to park their car in one of the peripheral car parks. During their stay, they move on foot, by bicycle or by electric boat in the park. So everyone can make the most of nature and water. “The LRM gave us the mission of distinguishing the houses in terms of number of guests, level of luxury and access to water. There are thus five basic types in terms of the number of people per house, from 2 to 12. The majority of the cottages are fully equipped, with air conditioning and a bathroom per room, but there are also several VIP accommodations with sauna, TV in room etc. All the houses have a pontoon that leads them directly to the water, each house also has a unique location. Finally, several homes have been designed for accessibility, with modifications for residents with disabilities.” adds Tractebel's Project Manager.
Photo : Sourbron Fotografie
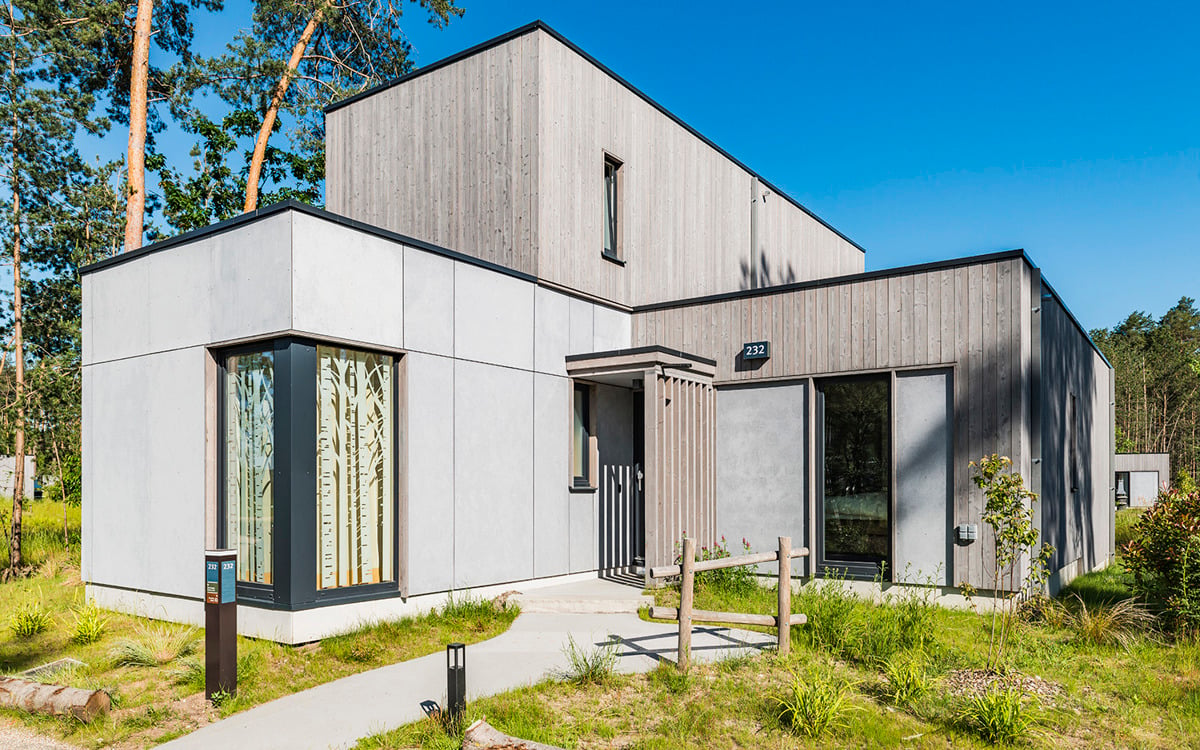
Indispensable durability
Everything has been designed with the audience in mind. The objective was to create a green and warm project, also with an important role for the ecological aspect. All homes are thus completely free from fossil fuels. The resort's electricity supply is 100% supplied by renewable energies, 30% of which is on site thanks to two parks of photovoltaic panels. To supply the cottages with energy, Tractebel has relied exclusively on electricity to avoid any local emissions. All means of transport in the park are electric (service vehicles, boats, golf carts, shuttle, ...) and the stove is also electrically powered. Rainwater is 100% infiltrated on site through canals and plans. water and heating of the central swimming pool is provided by a cogeneration installation. The choice of materials was also made according to this particular project, without sacrificing quality and luxury. Bart Moors: “We had to take into account several important elements for the facade materials. In a natural environment like this, it is important to think about the influence of the sun and water. With the shadow created by the trees, not all facades are illuminated uniformly, which can eventually reveal many shades of colour. Taking these factors into account, our choice very quickly fell on EQUITONE and its facade panels [tectiva], among the best on the market in terms of value for money. Due to inclement weather, we opted for a light grey variant. Thanks to their natural appearance, the panels blend in perfectly with the surroundings. The combination with the thermowood really creates a nice aesthetic. I had already often had the opportunity to work with EQUITONE, but never on such a scale and for this kind of application. I can say without any hesitation that EQUITONE offers excellent products, which are at the same time reliable, have limited combustibility , efficient and at a reasonable price. The EQUITONE [tectiva] panels corresponded perfectly to the result we wanted in terms of colour and texture."
Photo : Sourbron Fotografie
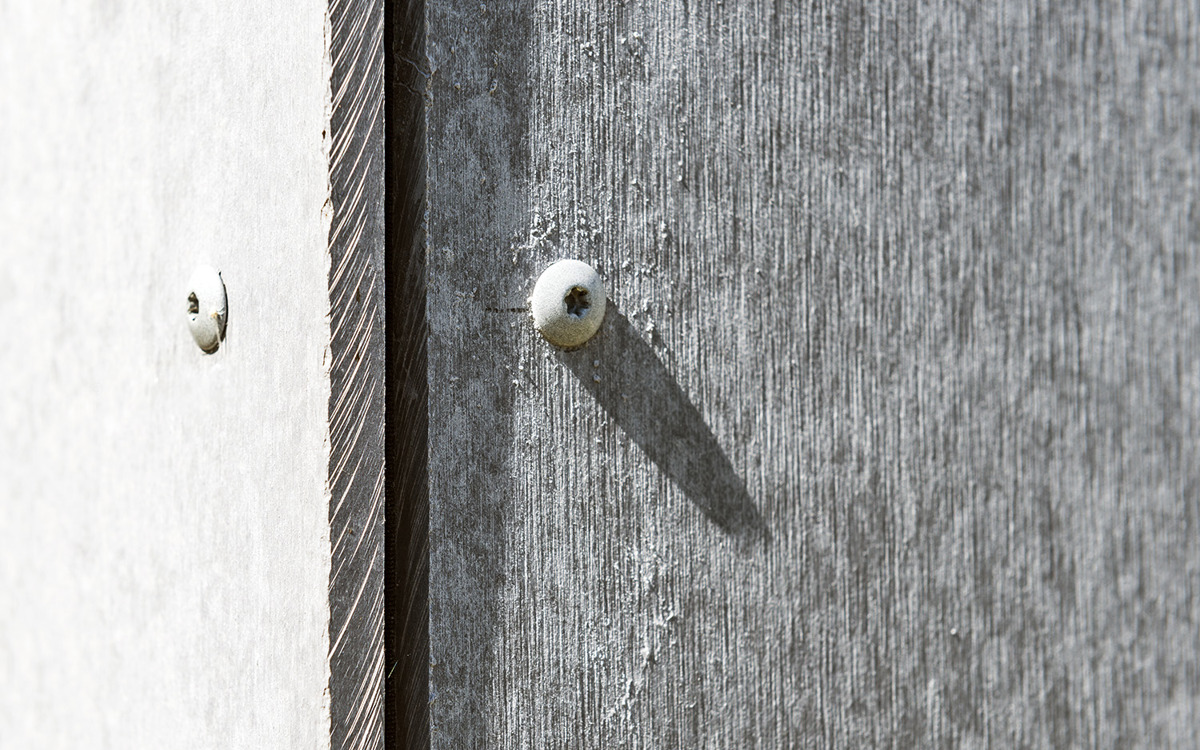
Disassemble and reuse
The modular and circular appearance of the facade was very important. Both EQUITONE and thermowood panels are easy to maintain and replace. “The circular aspect lies in the separation of the lots. We have knowingly separated the FF&E tenders (furniture, fixtures & equipment), finishes and wood frame to have different layers in terms of award and execution and thus allow various changes in the future. The assembly also remains removable. The facade can in our opinion remain in good condition for at least 50 years, but I suspect that a lot will have changed by then. By fixing the panels with screws rather than glue, we will be able to dismantle them more easily and reuse them for a second or even a third project ”, concludes Bart Moors from Tractebel.
Photo : Sourbron Fotografie