Open joints
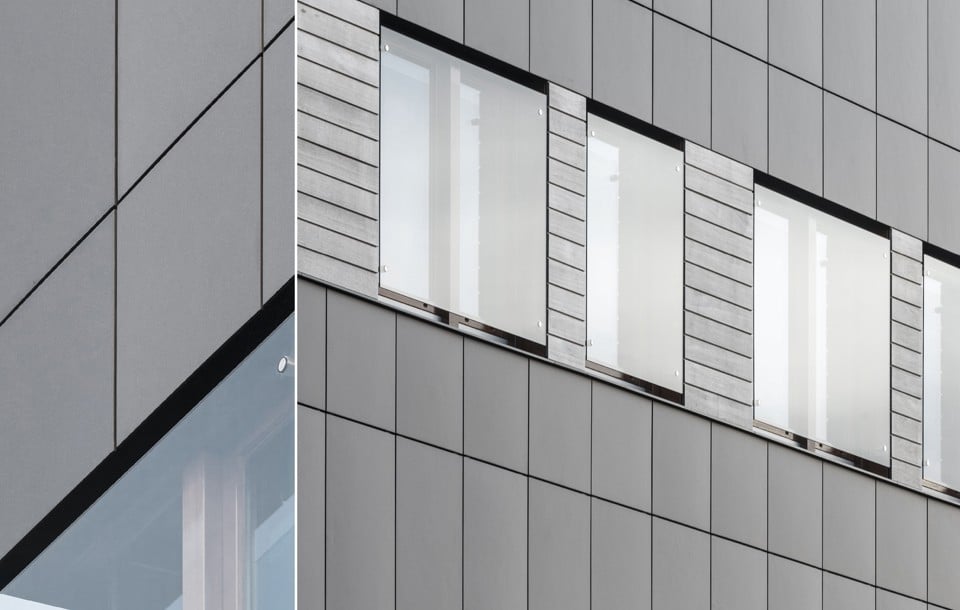
Open joints
in which there is a clear open gap between the edges of adjoining panels.
Consider colour choice of support frame, insulation and backing wall as these may be seen.
Joint Size
Many years of practice have shown that the optimum width of the joints between large panels is 10mm. A 10mm joint is the best, aesthetically. 10mm also offers the installer a good level of tolerance when installing the panel.
Minimum joint – 8mm. Maximum joint - 12mm
EQUITONE panels can be face fixed using EQUITONE UNI-rivet for metal support frames or the EQUITONE UNI-screw when a timber support frame is used. All fixings are available with colour match heads to blend in with the panel. The rivets and screws are both low profile heads.
The fixing systems are designed to accommodate the expansion and contraction of the support frame without putting excessive stresses on the panel.
The fixings are positioned at centres to suit the wind load the façade will be subjected to. Normally centres are up to 625mm and will reduce as determined by the wind calculations.
The corner position of the fixings should be located within the red box.
For hidden fixings a mechanical system is possible. Please note that this is a precision fixing system and a good knowledge of fabrication and installation is critical to ensure a successful facade.
Mechanical Secret
Fix The mechanical hanging system utilises an undercut anchor which is secured in the rear of the panel in specially drilled holes. To this a hanger bracket is fixed. This hanger then interlocks with a horizontal rail.
* Refer to the individual mechanical hanging systems installation literature for details. This system is suitable for EQUITONE [tectiva], EQUITONE [linea], and 12mm EQUITONE [natura], EQUITONE [natura PRO], EQUITONE [pictura], EQUITONE [textura] and EQUITONE [materia].
EQUITONE panels are strong yet light, which reduces the amount of supporting frame needed compared with other materials. Certification for the structural stability of any supporting frame should be in accordance with local building regulations and must be obtained by the building’s owner or his representatives namely the project engineer.
Common Support Frame Materials:
Structural Wall
The backing wall is critical to the performance of a ventilated facade system. If air movement through the backing wall is too great then the risk of water penetration is increased. Air leakage through the backing wall also presents a path for energy loss, and so must be limited.
General Principles:
Position the ends of the panels a minimum 150 mm above the finished ground level to:
No planting should be grown near the air inlet as over time the plants may block the air flow.
More information is contained in the application guidelines, contact technical support.
All façades, irrespective of the material used, should be serviced regularly. Then, unnecessary and high costs are avoided in the long term. The building also retains its continuous and attractive appearance. If one the allows the soiling to work into the materials for too long, it is possible that it will have penetrated so deeply into the pores of the material that simple cleaning is no longer possible The building should be designed with access in mind so all panel areas can be inspected and maintained.
Dust, soot, oils, greasy substances, etc. are present in the air and rainwater and can be deposited on a façade. If care is taken through considerate design and application, local soiling and runs can be avoided. This can be achieved by having adequate drip-moulding, good sealing and attention to combat corrodible materials such as zinc, copper, aluminium, steel, etc. The degree and speed at which materials become soiled largely depends on the surface, chemical stability, hardness, porosity, ability to become electrostatically charged or not.
Consideration should be given to how the building may weather and the how the water run-off from materials affects other materials below.
The UV-cured EQUITONE [pictura] and EQUITONE [natura pro] surface coating provides superior protection against common colours and spray paints. It is smooth and cleanable. The [pictura] and [natura pro] surface coating meets the requirements of the placement test and test cycle 2 of the Quality Association for Anti-Graffiti eV for surface-protective anti-graffiti systems (ILF 4-013/2006 report of the Institute for paints and inks eV). Note that when an on-site graffiti protection is applied to the panels the appearance of the panel may change as the protection effects the light reflectance of the panel’s colour.
There are two methods of cleaning façades, mechanical cleaning and chemical cleaning. In principle, perform the cleaning of the facade over the entire surface, because partial cleaning can result in colour tone differences.
Normal stains can be removed with a sponge and water. The use of abrasive materials such as scourer, steel wool, etc. is not allowed, as they leave irreparable scratches on the surface.
Lime scumming can be avoided by handling the sheets in the correct way. The sheets must be stacked in a dry ventilated space. The sheets must always be protected from rain. During storage the synthetic film may not be removed; the foil is only removed with use. If the sheets do become wet in the packing, all packaging must be removed and the sheets must be rubbed dry and placed in a way that they can dry out thoroughly. If lime scumming still occurs, one can remove it with a light acid solution, only applied to the sheet (not to glass, aluminium, etc.).
More information is contained in the application guidelines, contact technical support.